Article published May 2008:

Click here to
view the complete article.
Article published April 2007:
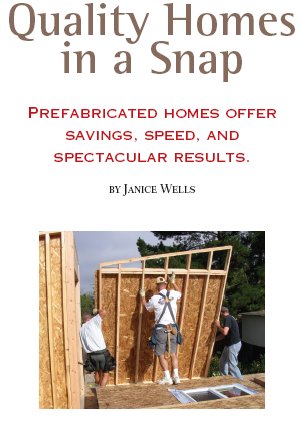
Click here to
view the complete article.
Article published January 2007:
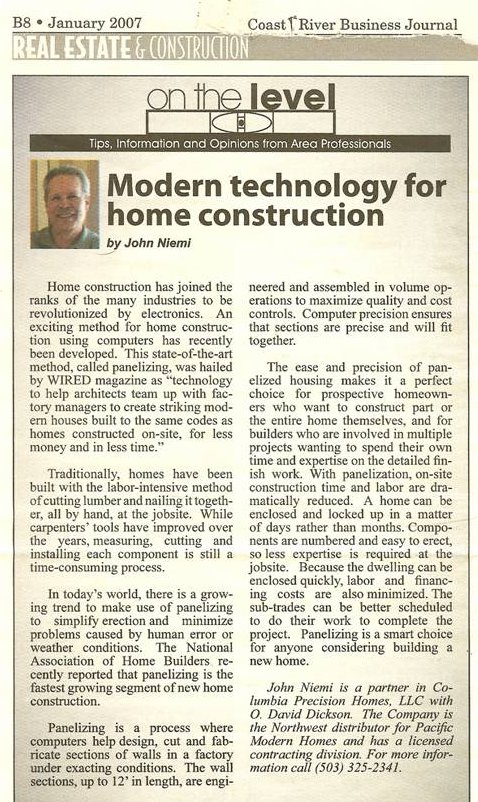
Book published in 2005, by the Taunton Press:
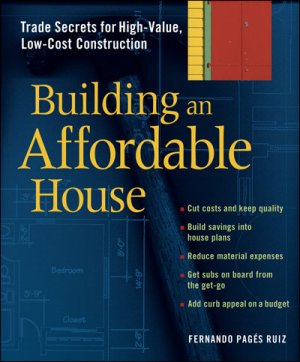 |
Building an Affordable House is a
very useful book, full of examples and suggestions about how
to build your new home more economically. The approaches to
construction outlined in the book are NOT about sweat
equity, purchasing schemes, or unproven technologies. The
book is about hard-nosed approaches to saving money, through
knowledge and better construction techniques.
So, why would we suggest this book?
Simple, one of the construction techniques suggested is the
use of wall panels and roof trusses. The author, Fernando
Pages Ruiz, even goes so far as to predict, "Prefabrication
is the future".
Mr. Ruiz further explains his belief in
wall panels in an article he wrote for the March 2005 issue
of Fine Homebuilding titled "Better Framing with
Factory-Built Walls".
|
Article published January, 2007:
Per the graph at right,
from Automated Builder, based upon 3.024 million homes built
in America in 2006: 47% of the homes were panelized (many
by PMHI) and 43% of the homes were job site built or stick built.
But, when you include the
factory built modulars and mobile homes (HUD-Code) 57% of
all the homes built in America in 2006 were some form of "industrialized"
or partially factory built.
There are reasons for
this:
-
Faster construction
time
-
Lower costs
-
Better quality
|
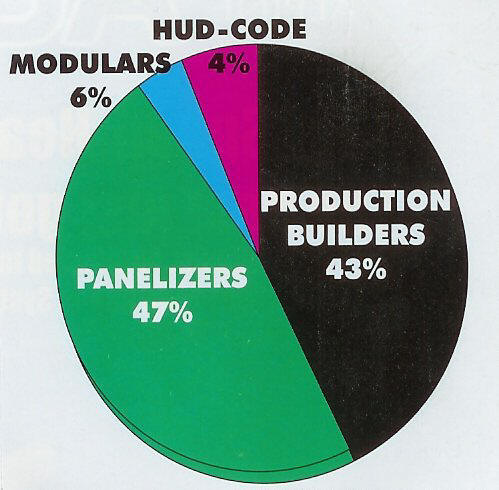 |
-
Article
published March 19, 2003:

Serving
Western Nevada County, CA
Couple saves time, money with
panels
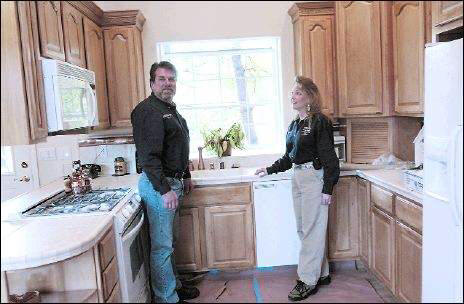 |
Using the construction equivalent of
paint by numbers saved Ken and Julie Zuckerman about
$8,000.The Grass Valley couple decided to use wall
panels manufactured in an Elk Grove factory for a
1,000-square-foot house the couple built for Julie's
mother.
Mike Leslie, the Zuckermans' contractor, gave them a bid
using several different types of construction, one of
them using prefabricated wall panels with windows and
doors already installed. "I was thinking about the
quality aspect because the walls are built in a
controlled environment," Ken Zuckerman said. But the savings were another reason the Zuckermans opted
to use the time-saving construction method.
Leslie, owner of Tekton Construction in
Auburn, ordered the wall panels through Auburn firm
Perma-Dwell, one of 15 domestic Pacific Modern Homes,
Inc. dealers, in mid-August. It usually takes four to
five weeks, six in the summer, for panels to be
delivered to construction sites, said Denise Dugger,
co-owner of Perma-Dwell. |
Gary
and Denise Dugger, owners of Perma-Dwell homes of
Auburn, are in the kitchen of their new home built on
Loma Rica Drive. |
|
Pacific Modern Home's wall panels,
which are up to 12 feet long and 8- to 10-feet-high,
arrive on the site with windows and doors already
installed. The Zuckermans used 10-foot by 12-foot
sections that arrived on an 18-wheel truck in the
couple's Wawona Madrona neighborhood near the airport. Panels are numbered so contractors can put the frame
together quickly. Because the walls are already
constructed and easy to fit together, it often saves
half to two-thirds the number of labor hours. Price
lists for dozens of plans are listed on the Pacific
Modern Home, Inc. Web site at
www.pmhi.com. |
All the walls of the Zuckermans'
1,000-square-foot, two-bedroom, two-bath home were up
within three days. "The neighbors couldn't believe it,"
Julie Zuckerman said. Their house used 32 panels, some
as small as 3 feet in width, Leslie said.
Pacific Modern Homes, Inc. describes its method of
building as environmentally responsible because far less
energy is needed to manufacture lumber than other
building materials. "Nine times less energy is used to
produce a wood 2-by-4 than a steel stud, and 24 times
less energy for a wood-framed floor than a concrete
floor," the firm's material states.
Another advantage of factory framing is that framing
packages allow owners to be in control of the
construction of their dream homes, Dugger said. Leslie
agreed. "A lot of clients want to come play on the
team," Leslie said. "They want the thrill of putting
their hand into the home they're going to live in."
|
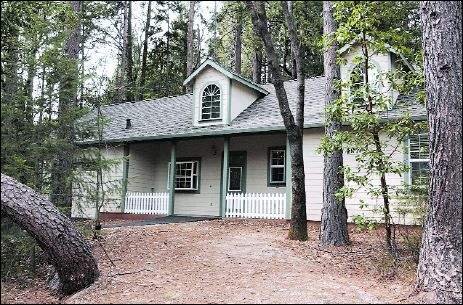 |
|
The
finished Perma-Dwell home on Loma Rica Drive owned by
Ken and Julie Zuckerman. |
|